By Nirmal John
3D Printing: The Ultimate Guide to Additive Manufacturing
Thursday April 17, 2025
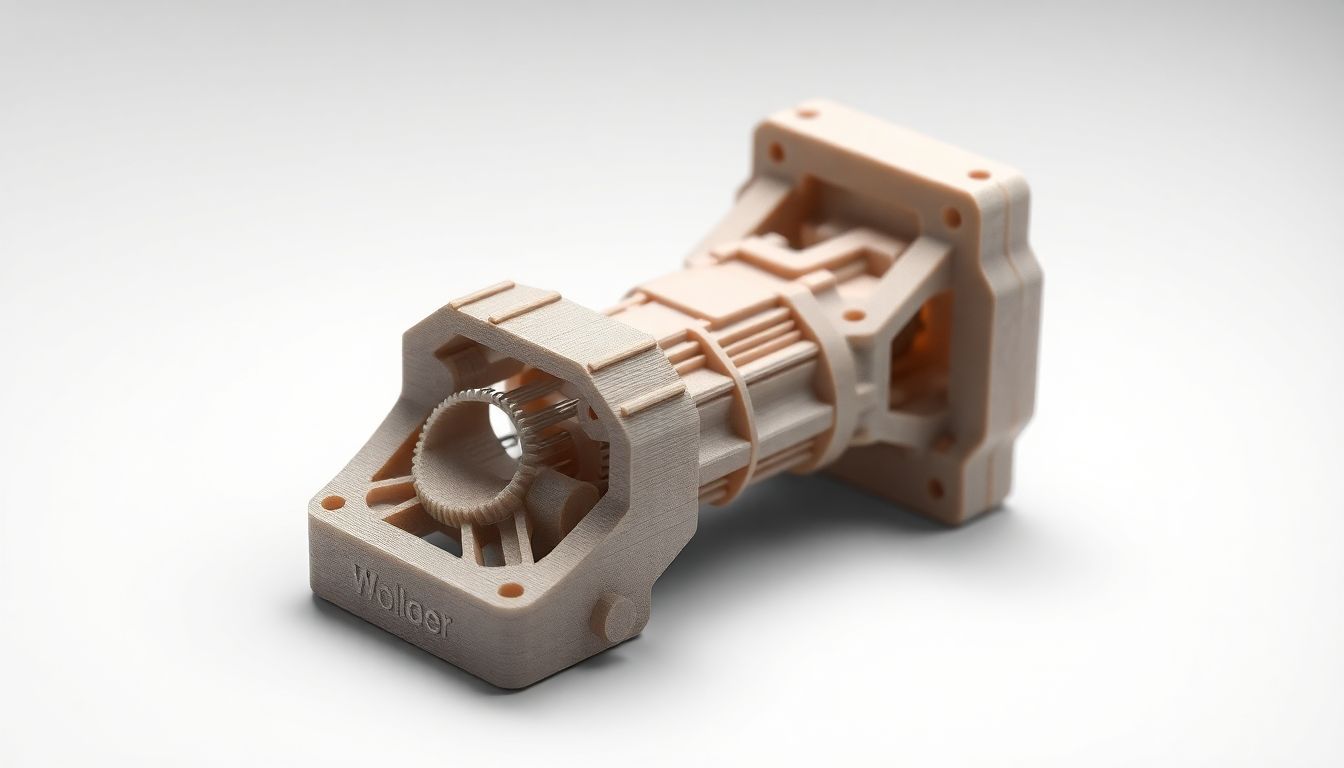
3D Printing: The Ultimate Guide to Additive Manufacturing
Imagine a surgeon holding a perfect replica of a patient’s heart, created specifically for pre-surgical planning. This isn’t science fiction—it’s the transformative power of 3D printing. This revolutionary technology, also known as additive manufacturing, constructs objects layer by layer from digital designs, fundamentally changing how products are conceived, produced, and utilized across numerous industries.
3D printing technology has evolved from a niche prototyping tool to a mainstream manufacturing method that’s reshaping everything from medical procedures to aerospace engineering. In this comprehensive guide, we’ll explore how 3D printing works, the various technologies and materials available, and its wide-ranging applications across different sectors.
What is 3D Printing and How Does it Work?
3D printing functions like building with digital building blocks. Unlike traditional manufacturing methods that remove material, 3D printing adds material layer by layer. This innovative approach enables the creation of virtually anything—from simple toys to complex aerospace components. Let’s examine the fundamental concepts and processes behind this technology.
Additive vs. Subtractive Manufacturing: Understanding the Difference
Traditional manufacturing typically follows a subtractive approach—imagine sculpting a statue from a block of stone, where you begin with excess material and remove what’s unnecessary. 3D printing represents the opposite philosophy:
- Subtractive manufacturing: Starts with a solid block and removes material until the desired shape emerges
- Additive manufacturing (3D printing): Begins with nothing and systematically adds material to create the final product
This additive approach offers several significant advantages:
- Reduced material waste: Only the necessary material is used, minimizing scrap
- Greater design freedom: Allows for complex geometries that would be impossible with traditional methods
- Cost-effective customization: Enables affordable production of personalized items
- Faster prototyping: Reduces development time from concept to physical model
The 3D Printing Process: A Step-by-Step Breakdown
The 3D printing process follows a structured workflow that transforms digital ideas into physical objects:
- Design creation: Using Computer-Aided Design (CAD) software, designers create a three-dimensional model of the object. Popular CAD programs include Fusion 360, SolidWorks, Blender, and TinkerCAD.
- File preparation: The design is exported as an STL (stereolithography) or OBJ file, which represents the object’s surface geometry.
- Slicing: Specialized software “slices” the model into hundreds or thousands of horizontal layers, creating a set of instructions (G-code) for the printer to follow.
- Printing: The 3D printer builds the object layer by layer according to the instructions, with each layer bonding to the previous one.
- Post-processing: Many printed objects require finishing touches, such as removing support structures, sanding rough surfaces, or applying coatings for improved appearance or functionality.
For optimal results, consider these technical aspects when preparing your 3D printing project:
- File resolution: Higher polygon counts in your STL files result in smoother curves but larger file sizes
- Layer height: Thinner layers create smoother surfaces but increase printing time
- Print orientation: How you position the model affects strength, surface quality, and support requirements
- Infill density: The percentage of solid material inside the object, affecting strength and material usage
Types of 3D Printing Technologies
The term “3D printing” encompasses a variety of technologies, each with unique characteristics suited to different applications. Here are the primary methods revolutionizing manufacturing today:
Fused Deposition Modeling (FDM): Accessible and Versatile
FDM represents the most widely adopted 3D printing technology, particularly in consumer and educational markets. It operates on straightforward principles:
- A thermoplastic filament is heated to its melting point
- The liquefied plastic is extruded through a nozzle
- The printer deposits the material precisely, layer by layer
- Each layer cools and solidifies before the next is applied
Popular materials for FDM include:
- PLA (Polylactic Acid): Biodegradable, easy to print, ideal for beginners
- ABS (Acrylonitrile Butadiene Styrene): Durable and heat-resistant, but requires ventilation
- PETG (Polyethylene Terephthalate Glycol): Food-safe, durable, and less prone to warping
FDM technology is especially valuable for:
- Affordable prototyping
- Educational projects
- Hobbyist applications
- Basic functional parts
- Quick concept models
Stereolithography (SLA): Precision and Detail
SLA technology delivers significantly higher resolution than FDM, making it ideal for applications requiring fine details:
- A vat contains liquid photopolymer resin
- A UV laser beam selectively hardens specific areas of the resin
- The build platform adjusts after each layer is cured
- The process repeats until the object is complete
SLA prints are characterized by:
- Exceptional surface smoothness
- High dimensional accuracy
- Fine feature reproduction
- Isotropic mechanical properties
This technology excels in applications such as:
- Jewelry design and production
- Dental models and surgical guides
- Highly detailed architectural models
- Custom hearing aids
- Intricate prototypes with fine features
Selective Laser Sintering (SLS): Strong, Complex Parts
SLS technology offers unique capabilities for producing complex, functional components:
- A thin layer of powdered material is spread across the build platform
- A high-powered laser selectively fuses the particles together
- After each layer is completed, fresh powder is spread
- Unfused powder supports the structure during printing
Key advantages of SLS include:
- No need for support structures
- High mechanical strength
- Ability to create interlocking or moving parts in a single print
- Wide range of available materials
SLS is commonly employed for:
- Functional prototypes
- Small-batch production parts
- Complex assemblies
- Aerospace components
- Automotive parts
Other Notable 3D Printing Technologies
The 3D printing ecosystem continues to expand with specialized technologies:
- Digital Light Processing (DLP): Similar to SLA but uses a digital projector instead of a laser, offering faster build speeds
- Multi Jet Fusion (MJF): Uses inkjet arrays to apply fusing and detailing agents to powder, then fuses entire layers at once
- Direct Metal Laser Sintering (DMLS): Creates fully dense metal parts directly from digital files
- Binder Jetting: Deposits liquid binding agents onto powder materials, creating parts or molds
Materials Used in 3D Printing
The versatility of 3D printing is amplified by the expanding range of available materials. From common plastics to exotic alloys, the material selection affects functionality, durability, appearance, and cost.
Plastics and Polymers: The Foundation of 3D Printing
Polymers represent the most widely used category of 3D printing materials due to their accessibility and versatility:
Standard Thermoplastics:
- PLA: Derived from renewable resources like corn starch, PLA offers ease of printing, biodegradability, and low toxicity. Ideal for decorative items and prototypes not exposed to heat.
- ABS: Known for durability and heat resistance, ABS is popular for functional parts but requires higher printing temperatures and often a heated enclosure.
- PETG: Combines strength with flexibility and chemical resistance, making it suitable for food containers and mechanical parts.
- TPU (Thermoplastic Polyurethane): Highly flexible and elastic, perfect for phone cases, shoe soles, and other applications requiring bendable properties.
Engineering Polymers:
- Nylon: Offers excellent strength-to-weight ratio and durability, with natural flexibility and impact resistance.
- Polycarbonate: Features optical clarity and extraordinary impact strength, used in demanding applications.
- PEEK (Polyether Ether Ketone): An ultra-high-performance polymer with exceptional heat and chemical resistance, suitable for aerospace and medical applications.
Composite Filaments:
- Wood-infused filaments that produce prints with a natural wooden appearance
- Carbon fiber-reinforced materials for enhanced strength and stiffness
- Metal-filled polymers that mimic metallic appearance and weight
Metals: Industrial-Strength Solutions
Metal 3D printing has revolutionized industries requiring high-performance, durable components:
Common Metal Materials:
- Aluminum alloys: Lightweight yet strong, with excellent thermal properties
- Stainless steel: Corrosion-resistant and durable, suitable for medical and food-safe applications
- Titanium: Exceptional strength-to-weight ratio, biocompatible, used in aerospace and medical implants
- Inconel: Super alloys for high-temperature applications
- Tool steels: For industrial tooling and injection molds
Metal 3D printing technologies include DMLS, Selective Laser Melting (SLM), and Electron Beam Melting (EBM), each offering specific advantages for different applications.
Composites and Ceramics: Specialized Materials
As 3D printing evolves, more exotic materials continue to expand the technology’s capabilities:
Composite Materials:
- Carbon fiber composites that deliver exceptional strength with minimal weight
- Fiberglass-reinforced polymers for electrical insulation and structural applications
- Kevlar-infused filaments for ballistic protection applications
Ceramics:
- Technical ceramics for high-temperature applications
- Bioceramics for medical implants
- Ceramic-polymer composites that combine the benefits of both material types
Other Materials:
- Wax for investment casting
- Food-grade materials for culinary applications
- Biocompatible resins for dental and medical purposes
3D Printing Applications Across Industries
The versatility of 3D printing has led to its adoption across diverse sectors, each leveraging unique aspects of the technology.
Healthcare: Personalizing Patient Care
3D printing is transforming healthcare through customization and rapid production:
Prosthetics and Orthotics:
- Custom-fitted prosthetic limbs at significantly lower costs
- Personalized orthotic devices tailored to individual patients
- Improved comfort and functionality through precise anatomical matching
Surgical Planning and Education:
- Anatomical models created from patient CT scans for pre-surgical planning
- Reduced operating times and improved outcomes through better preparation
- Training tools for medical students and surgical residents
Bioprinting and Implants:
- Custom titanium implants that perfectly match patient anatomy
- 3D-printed surgical guides that improve placement accuracy
- Experimental bioprinting of tissues and organs using living cells
- Patient-specific hearing aids and dental products
According to a report by Grand View Research, the medical 3D printing market is expected to reach $3.5 billion by 2025, growing at a compound annual growth rate of 17.7%.
Aerospace: Lightweighting and Integration
The aerospace industry has embraced 3D printing for its ability to create complex, lightweight components:
Advanced Components:
- Fuel nozzles with integrated cooling channels that were impossible to manufacture traditionally
- Lightweight structural components that reduce fuel consumption
- Consolidated assemblies that reduce part count and improve reliability
Cost and Time Benefits:
- Reduced lead times for specialized parts
- Lower material waste in manufacturing expensive aerospace alloys
- On-demand production for obsolete parts or remote locations
Major aerospace manufacturers like GE Aviation, Boeing, and SpaceX have incorporated 3D printing into their production processes, with GE’s advanced turboprop engine consolidating 855 parts into just 12 3D-printed components.
Manufacturing: Reimagining Production
Traditional manufacturing is being enhanced and sometimes replaced by 3D printing applications:
Rapid Prototyping:
- Faster design iterations and development cycles
- Reduced costs for testing multiple design variants
- Improved communication between design and engineering teams
Tooling and Fixtures:
- Custom jigs and fixtures that improve assembly processes
- 3D-printed injection molds for small production runs
- Specialized tools for unique manufacturing challenges
End-Use Production:
- Mass customization of consumer products
- Small-batch production without traditional tooling costs
- Just-in-time manufacturing that reduces inventory requirements
Supply Chain Implications:
- Localized production closer to end users
- Reduced shipping costs and environmental impact
- Simplified inventory management through on-demand production
Other Industries Embracing 3D Printing
The innovation extends well beyond the major adopters:
Architecture and Construction:
- Detailed architectural models with complex features
- Experimental building components and full-scale structures
- Custom interior design elements and fixtures
Education:
- Hands-on learning tools for STEM education
- Visualization of complex scientific concepts
- Affordable prototyping for student projects
Automotive:
- Custom parts for classic car restoration
- Performance parts for racing applications
- Rapid prototyping of design concepts
Consumer Products:
- Customized household items and gadgets
- Limited edition designer products
- Replacement parts for discontinued products
The Future of 3D Printing
As 3D printing technology continues to mature, several key developments are shaping its evolution:
Advancements in Materials Science
The frontier of 3D printing innovation lies largely in materials development:
Biocompatible Materials:
- Resorbable implants that safely dissolve in the body
- Custom pharmaceutical formulations with tailored release profiles
- Advanced biomaterials that promote tissue integration
Smart Materials:
- 4D printing using materials that change shape in response to stimuli
- Embedded electronics within printed structures
- Self-healing materials that repair damage automatically
High-Performance Polymers:
- Materials with exceptional heat resistance for demanding applications
- Electrically conductive polymers for printed electronics
- Ultra-lightweight yet strong composites for aerospace and automotive
3D Printing at Industrial Scale
The technology is transitioning from prototyping to full-scale production:
Mass Customization:
- Economically viable personalization of consumer products
- Individual-specific medical devices and tools
- Custom-fit clothing and footwear
Distributed Manufacturing:
- Local production hubs instead of centralized factories
- Reduced shipping and inventory costs
- Faster response to market demands and changes
Sustainability Benefits:
- Reduced material waste compared to traditional manufacturing
- Lower transportation emissions through localized production
- Improved repairability through on-demand spare parts
“3D printing will revolutionize manufacturing by enabling on-demand production of customized products, fundamentally changing supply chains,” says Dr. Emily Carter, a leading materials scientist. “We’re moving from an era of mass production to one of mass customization, with profound implications for how businesses operate.”
Emerging Applications and Technologies
The horizon of 3D printing continues to expand:
Construction 3D Printing:
- Large-scale printers creating building components or entire structures
- Reduced construction waste and faster building times
- Architectural designs that would be impossible with traditional methods
Food Printing:
- Customized nutrition based on individual needs
- Complex food geometries and presentations
- Alternative protein formulations with improved texture
Multi-Material and Multi-Process Printing:
- Combining different materials in a single print
- Integrating electronics and mechanical components
- Hybrid manufacturing cells that combine additive and subtractive processes
Space Applications:
- In-orbit manufacturing of replacement parts
- 3D printing habitats on the Moon or Mars using local materials
- Production of tools and equipment for space exploration
Getting Started with 3D Printing
For those interested in exploring 3D printing firsthand:
Choosing Your First 3D Printer
Consider these factors when selecting a printer:
- Budget: Entry-level FDM printers start around $200, while professional systems can cost thousands
- Build volume: Determine the maximum size of objects you’ll need to print
- Print quality: Higher resolution printers produce finer details but often at higher cost
- Materials compatibility: Ensure the printer works with the materials you plan to use
- Community support: Look for printers with active user communities for troubleshooting help
Popular beginner options include the Creality Ender 3, Prusa Mini, and Anycubic Photon Mono.
Essential Software for 3D Printing
A complete 3D printing workflow requires:
- Design software: Fusion 360, Blender, TinkerCAD, or FreeCAD
- Slicing software: Cura, PrusaSlicer, or Simplify3D
- File repair tools: Meshmixer or Netfabb for fixing model issues
- Model repositories: Thingiverse, Printables, or MyMiniFactory for ready-to-print designs
Learning Resources and Communities
To develop your 3D printing skills:
- Online courses on Coursera, Udemy, or YouTube
- Local makerspace workshops and classes
- Online forums like r/3Dprinting or the 3D Printing Discord
- Industry publications and blogs like All3DP and 3DPrint.com
Conclusion: The Transformative Impact of 3D Printing
3D printing represents more than just a technological advancement—it embodies a fundamental shift in how we conceptualize design and manufacturing. From revolutionizing healthcare with patient-specific solutions to transforming aerospace with integrated lightweight components, the technology continues to expand its influence across industries.
As materials improve, costs decrease, and processes become more efficient, 3D printing will continue its journey from specialized tool to mainstream manufacturing method. The democratization of production capabilities is already enabling innovation at unprecedented rates, with designers and engineers unbound by traditional manufacturing constraints.
Whether you’re a hobbyist interested in personal projects, an educator introducing students to future technologies, or a business professional exploring new production methods, 3D printing offers unique opportunities to turn digital concepts into physical reality.
The future of manufacturing is taking shape, layer by layer. Are you ready to be part of the 3D printing revolution?
About the author
Recent articles
Quad Core Dedicated Servers
Interested in Quad Core Dedicated Servers? View our inventory. What is a quad core dedicated...
Read More8 Core Dedicated Servers
For website owners looking to eliminate their hardware bottlenecks, the massive power capabilities of an...
Read MoreHow Unmetered Servers Can Help Businesses Grow
If you have a business website that is growing and expanding, it is essential that...
Read More